"Acero verde": Lograr la siderurgia sostenible requiere pequeños pasos y grandes saltos
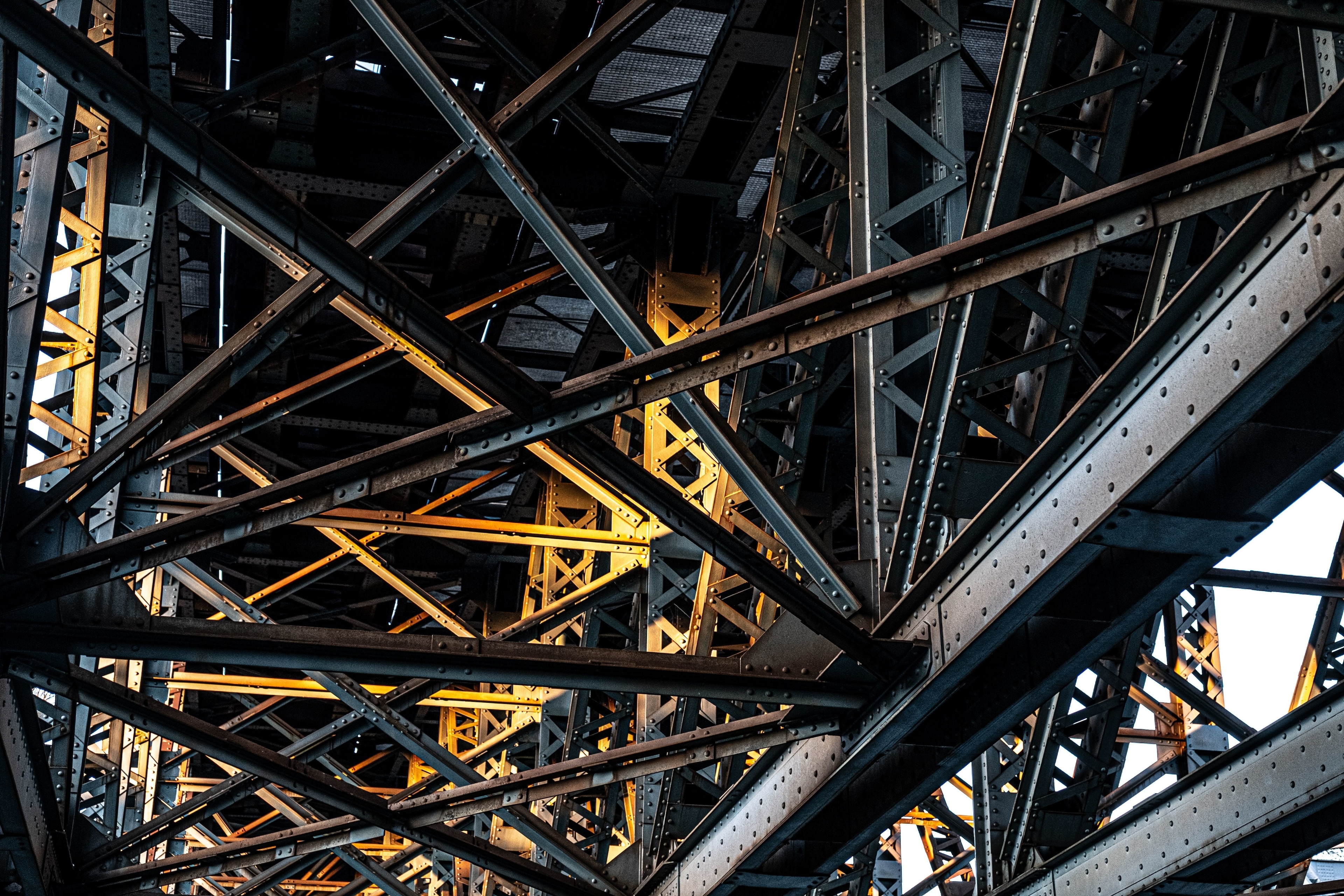
Es hora de impulsar la industria siderúrgica ecológica.
Image: Unsplash/Luca Upper
Mantente al día:
SDG 07: Energía limpia y asequible
Listen to the article
- El acero es un ingrediente clave en el mundo moderno: utilizado en todo, desde edificios a bicicletas, pero muy intensivo en CO2.
- El mayor salto en la ecologización de la industria siderúrgica procede de fuentes de energía y métodos de producción más limpios, con un futuro que mira hacia las tecnologías ligeras en carbono.
- La huella de carbono de la producción europea de acero puede reducirse significativamente mediante la localización de la materia prima.
El acero -un ingrediente clave de nuestro mundo moderno, que se utiliza en todo tipo de materiales, desde edificios hasta bicicletas- es muy intensivo en CO2. Su producción es responsable de alrededor del 5% de las emisiones de CO2 en la UE y del 7% en todo el mundo.
No podemos vivir sin él, pero, ¿cómo podemos vivir con él? Tenemos que dar saltos -grandes, caros y complicados- para generar enormes beneficios a través del acero ecológico. Simultáneamente, tenemos que dar pasos más pequeños, fáciles y rápidos hacia un acero más ecológico.
Los grandes cambios, como el paso de la iluminación de gas a la eléctrica, pueden tardar décadas en aplicarse e implicar nuevas infraestructuras masivas. Pero las mejoras graduales también pueden tener un gran impacto y, al mismo tiempo, ser sencillas y poco costosas. Un ejemplo es la optimización de la eficiencia de la combustión: cuando se mezcla la cantidad justa de oxígeno con el gas natural, se obtiene la llama azul, caliente y limpia de una estufa moderna, en lugar de la llama amarilla de hollín de un quemador no regulado.
Con suficientes pasos, podemos escalar una montaña. Sólo tenemos que asegurarnos de que los pasos van en la dirección correcta.
El Pacto Verde de la UE impulsa la acción
El Pacto Verde europeo está impulsando a las industrias a examinar sus procesos y cadenas de suministro para comprender mejor dónde se producen sus emisiones de CO2 y cómo reducir la huella global. La tecnología es un motor clave en este ejercicio, ya que ayuda a las empresas a recopilar los datos que necesitan, no sólo de sus propias operaciones, sino también de las de toda su cadena de suministro. Las empresas necesitan datos para saber que sus pasos las llevan en la dirección correcta.
Para la industria siderúrgica, el mayor salto hacia la ecologización procede de las fuentes de energía y los métodos de producción, con un futuro que mira hacia tecnologías ligeras en carbono, como la producción directa de hierro reducido en carbono (HRD) con hidrógeno, frente a los altos hornos de carbón (AH).
Alrededor del 60% de la producción europea de acero se basa en la producción de hierro AH a partir de mineral de hierro, con lo que una tonelada de acero supone alrededor de 1,9 toneladas de emisiones de CO2. El 40% restante de la producción europea de acero se obtiene a partir de HRD alimentado con gas natural, en algunos casos utilizando chatarra reciclada como materia prima, lo que supone unas emisiones más modestas de entre 1,4 y 0,4 toneladas de CO2 por tonelada de acero. Es importante destacar que este proceso más circular, que utiliza material reciclado, es más ecológico, pero el metal resultante se considera inferior y sólo es apto para determinadas aplicaciones.
El hidrógeno verde puede impulsar al acero verde
Para dar el mayor salto hacia el acero ecológico es necesario sustituir el gas natural por hidrógeno en una planta de HRD. Pero no cualquier hidrógeno: debe ser hidrógeno "verde". Hoy en día, la gran mayoría del hidrógeno se produce en un proceso que utiliza gas natural, lo que se conoce como hidrógeno "gris". Para que una planta de HRD sea realmente ecológica, debe alimentarse con hidrógeno verde, producido mediante electrólisis utilizando agua y electricidad de fuentes renovables, como la eólica y la solar.
La producción europea de acero de nueva generación se centra precisamente en esto. Mediante el uso de hidrógeno verde y circuitos de producción de HRD, el objetivo es cerrar la brecha de aproximadamente 1,3 toneladas de CO2 por tonelada de acero que se deriva del uso de AH. Se espera que este enorme cambio requiera más de 180 000 millones de euros de inversión en plantas siderúrgicas, electrolizadores de hidrógeno y fuentes adicionales de energía renovable.
180 000 millones de euros es mucha inversión. Movilizar semejante montaña de capital -especialmente en un entorno de altos tipos de interés- requiere una compleja red de apoyo gubernamental, medidas reguladoras y audacia comercial. El trabajo está en marcha, pero lleva años.
Mientras tanto, ¿qué medidas podemos tomar?
Esta pregunta se la hizo recientemente Aethel Mining, que explota el segundo mayor yacimiento de hierro de Europa. Aethel Mining utiliza el software de Dorae - un Global Innovator (Innovador Global) del Foro Económico Mundial y anterior Technology Pioneer (Pionero Tecnológico) - para gestionar gran parte de sus operaciones cotidianas y sus esfuerzos de planificación de productos. Aethel Mining utilizó la información obtenida con Dorae -datos variados, desde horas de máquina hasta resultados de laboratorio y movimientos logísticos- para calcular la huella de carbono de sus propias operaciones y las de sus posibles vías de distribución, en comparación con otras cadenas de suministro de acero.
¿El resultado? La idea de que la huella de carbono de la producción europea de acero puede reducirse significativamente mediante la localización de las materias primas.
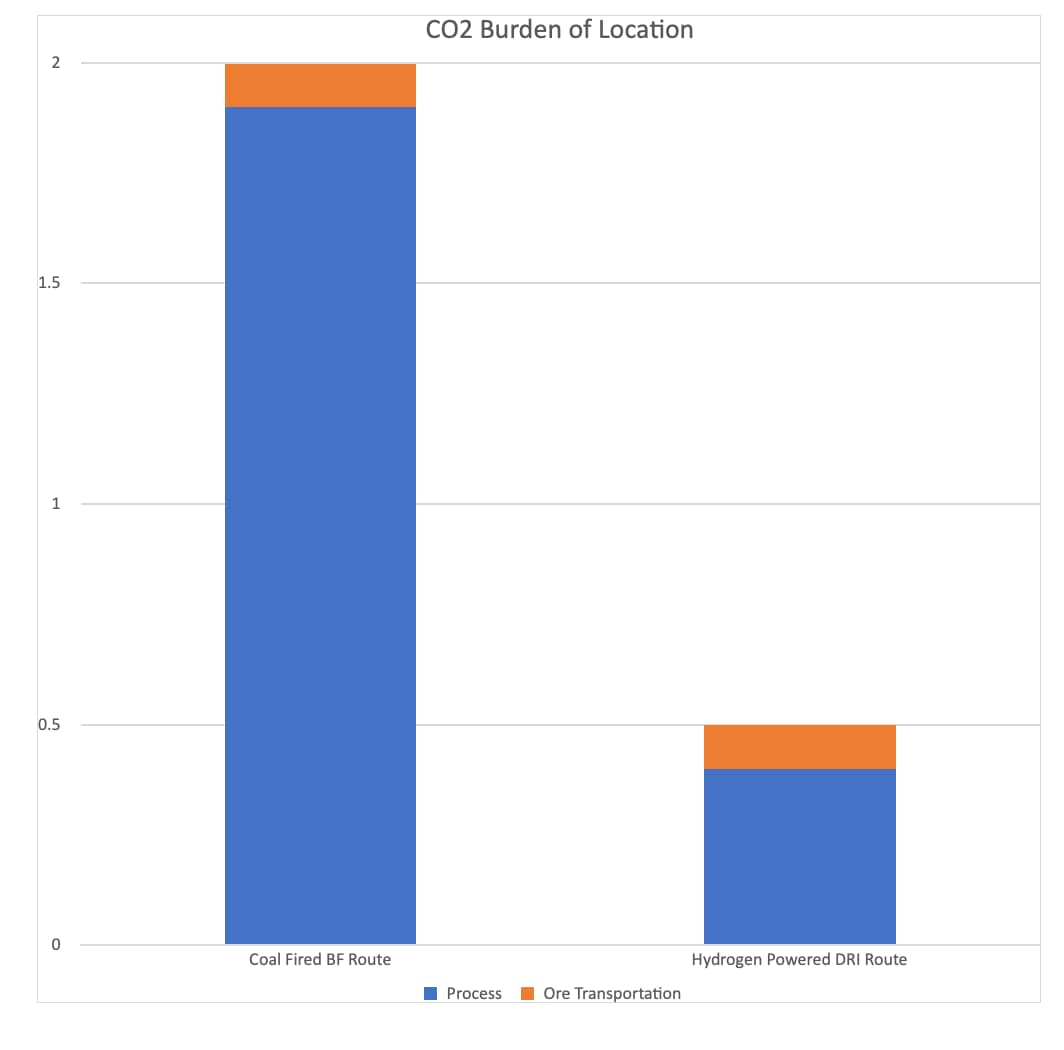
Gran parte del acero mundial se produce en China. Además de la energía necesaria para transformar el mineral de hierro en hierro y, a su vez, en acero, el mineral debe llegar al lugar de procesamiento. Un viaje de ida y vuelta a buen ritmo en un buque Capesize que transporte mineral de hierro de Brasil a China tarda unos 90 días y quema casi 3500 toneladas de fuelóleo. Esto equivale a unas 10 500 toneladas de CO2 durante el viaje y a 0,11 toneladas de CO2 por tonelada de metal producida a partir del mineral.
Reducir esta carga de emisiones puede no ser un gran salto, pero es un paso significativo. Al suministrar mineral de hierro desde el corazón de Europa, Aethel Mining puede aportar un ahorro de CO2 a la producción europea de acero. 0,11 toneladas es una fracción de las emisiones de CO2 a las que apuntan las nuevas infraestructuras energéticas e industriales, pero puede hacerse ahora, no dentro de años, y no cuesta 180 000 millones de euros. De hecho, ahorra dinero en transporte y la proximidad hace más fiable la cadena de suministro.
Como hicieron Faraday y Bunsen en el siglo XIX, podemos reunir y conectar la información para introducir mejoras graduales en cosas tan básicas como el fuego o la elección de un proveedor. La tecnología puede ayudarnos a ampliar y profundizar la red de información y a avanzar más rápido, de modo que podamos dar pequeños pasos inmediatos hacia la sostenibilidad, mientras trabajamos durante décadas en los grandes saltos.
Acepte nuestras cookies de marketing para acceder a este contenido.
Estas cookies están actualmente deshabilitadas en su navegador.
No te pierdas ninguna actualización sobre este tema
Crea una cuenta gratuita y accede a tu colección personalizada de contenidos con nuestras últimas publicaciones y análisis.
Licencia y republicación
Los artículos del Foro Económico Mundial pueden volver a publicarse de acuerdo con la Licencia Pública Internacional Creative Commons Reconocimiento-NoComercial-SinObraDerivada 4.0, y de acuerdo con nuestras condiciones de uso.
Las opiniones expresadas en este artículo son las del autor y no del Foro Económico Mundial.
Temas relacionados:
La Agenda Semanal
Una actualización semanal de los temas más importantes de la agenda global
Más sobre Naturaleza y BiodiversidadVer todo
Alfredo Giron
9 de mayo de 2025
Alejandra Arochas and Constanza Torres
6 de mayo de 2025
Victoria Masterson, Stephen Hall and Madeleine North
15 de abril de 2025
Nunzio Peleggi
3 de abril de 2025